La decisión de producir una parte en un herramental progresivo generalmente se determina basado en dos factores: el volumen de producción y la complejidad de la parte. Estos dos factores son fundamentales en el diseño y construcción de la herramienta. Es importante abordar todos los factores que pueden contribuir al nivel de calidad de la parte, mantenimiento y vida de la herramienta. La ponderación de los factores será necesaria para poder llegar a la mayoría de las decisiones finales y éstas afectarán el costo de la herramienta.
Orientación de la parte
El proceso comienza determinando la posición con la que la parte será corrida dentro del troquel. Esto es dominado por las características de la parte y de las posiciones de planos de referencia y tolerancias critica. Entonces el compromiso comienza.
Para optimizar el uso del material puede ser necesario girar la parte en la tira, esto cambiará la dirección del grano y puede afectar la resistencia de cualquier forma en la parte. Formado con el grano puede causar un rompimiento y fatiga del metal y será más difícil mantener consistentemente el formando ángulos. Por esto la forma será mucho más susceptible a problemas asociados con la composición química de cada una de las bobinas que se corran en el troquel.
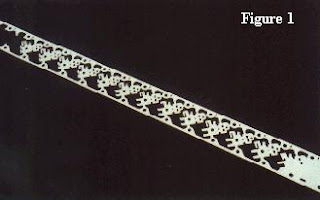
Figura 1. Esta parte se giró en la tira para mantener una mejo tolerancia crítica.
Por ejemplo en Figura 1 muestra una parte para la industria de la computación que fue girada en la tira para protegerla en contra el formado inconsistente de ángulos que pudiera ser causada por diferencias entre las bobinas. La parte contiene dimensiones críticas con tolerancias de .025mm que dependen de las formas. Girar la tira para asegurar figuras más consistentes no resulta en el uso más eficiente del material. Sin embargo en este caso, las tolerancias de la parte ganaron a la sobre optimización del uso del material.
La configuración de la parte puede proporcionar una segunda motivación para girar la parte en la tira. Si se requiere formado o perforado para producir la parte progresivamente, girar la parte puede se lo mejor y a veces es la única opción ya que la leva y el seguidor puede tomar una cantidad importante del espacio. La parte típicamente se gira para que el funcionamiento de las levas sea perpendicular a la bobina. Esto provee la condición más fácil y accesible para la levas.
Usualmente, un compromiso entre girar una parte para optimizar el uso del material y girar las levas para mantenerlas afuera de la bobina, es el resultado final. Esto puede aumentar el costo por pieza y los costos de herramienta. Sin embargo para producir la parte progresivamente dicho compromiso puede ser
necesario.
Una tercera consideración que puede requerir girar la parte en la tira es la cantidad de la elevación que es necesitaría para transportar la tira por el dado. La necesidad de elevar la tira se puede eliminar o reducir completamente al girar la parte apropiadamente.
Si todas las formas de la parte están en la misma dirección, el levantamiento se puede eliminar formando hacia arriba. Esto usualmente aumenta el costo del dado. Cuando la parte tiene formas en la dirección opuesta, se debe lograr un compromiso entre la elevación excesiva, uso de material óptimo, la complejidad de la herramienta y costo de la herramienta.
Tal compromiso se muestra en la Figura 2. La parte se transporta con un esqueleto tipo escalera, que agrega material al ancho de la bobina porque solo 2 pequeñas aéreas están disponibles para cargar la parte. También debido a la forma y longitud de las características, es necesario un aumento significativo en la elevación. Los elevadores de tira externos para transportar la tira tipo escalera trabajan bien en situaciones que requieren mucha altura.

La última consideración para orientar la parte dentro de la tira es girarla para que la alimentación sea tan corta como sea posible. Esto es especialmente importante para materiales más pesados y bobinas más estrechas. El corte longitudinal con cuchillas redondas puede causar una torcedura lateral (camber) en las bobinas que puede ser difícil de alimentar. Una progresión corta corre rápidamente y tiene menos oportunidad para causar problemas de alimentación. Cuando existe una diferencia substancial entre la longitud y el ancho de la parte, es usualmente más rentable para construir la herramienta con la menor alimentación (menor dimensión). .
Transportando la parte:
Como las partes son transportadas en la tira afecta la alimentación del dado, la habilidad para elevar la tira para alimentar y la habilidad de producir las partes con una calidad consistente. Tres opciones básicas están disponibles para transportar la parte, aunque se pueden usar muchas variaciones de cada una de éstas. En el método más directo, las partes son transportadas por el desperdicio entre ellas. El material excedente necesario que debe dejarse por lado para después ser recortado es igual a uno a dos de espesores de la lámina. Este método produce típicamente un mínimo de desperdicio.
Se requieren ciertas configuraciones en la parte para poder usar este método. Al girar y acomodar las partes de extremo a extremo, éstas deben tener suficiente área usable tanto en el borde delantero como en el borde trasero de la progresión. (ver Figura 3)

La segunda opción básica de tira, es aquella en la que la parte se transportada por un lado de la tira, esto se muestra en la Figura 3. Este estilo es adecuado para partes que requieren una gran demanda de formado en hasta tres lados. Esto también mejora la accesibilidad si se requiere se recorte o formado con levas.
Elevar la tira a por arriba del dado de la leva se vuelve más difícil, cuando se usa esta opción de transporte. Un elevador de material en la orilla de la tira no es
suficiente, se requieren elevadores en el centro de la tira para balancear o cuando alimentar la tira a través del dado puede ser un problema. Lograr una elevación apropiada que puede ser difícil cuando se tienen que formar dobleces grandes hacia abajo o se tienen que formar muchos dobleces.
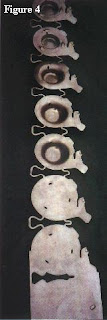
Este tipo de transportador puede causar otro problema de alimentación. El recorte de una gran cantidad de material de un lado de la bobina puede causar una deformación lateral (camber) en la tira cuando se libera los esfuerzos residuales del acero. Entre más progresiones tiene un dado aumentará el riesgo de problemas de alimentación y alineación de pilotos debidos a la deformación lateral de la tira (camber).
La configuración de la parte, el grosor del material y que tan estrecho debe ser el transportador son todos los factores que determinarán si la deformación lateral será un problema o no. Para prevenir la deformación lateral, Se debe aumentar el ancho de la bobina de manera que se pueda recortar el lado del esqueleto de la bobina. El recorte adicional libera tensiones desde el lado opuesto de la bobina y el equilibra la tira. Aun con éste corte adicional transportar la parte por un lado de la tira puede ser el método más efectivo para fabricar la parte desde punto de vista de aprovechamiento de material.
La tercera opción de transporte es la tira tipo escalera. Algunas de las ventajas del transporte tipo escalera que se discutieron anteriormente. Estos transportadores funcionan de manera correcta con partes complejas y con aquellas que requieren elevaciones significativas. Debido a que este método permite que la tira se alimente fácilmente, a menudo se utiliza para aplicaciones en los cuales se necesitan altas velocidades de alimentación.
El transportador de escalera usa mas material por parte. Sin embargo, a menudo la parte no puede producirse progresivamente por medio de otro método. Si el
volumen de producción están en el límite en términos de la justificación de la herramienta progresiva, el costo adicional del herramental y el desperdicio adicional de material, es posible que sea una mejor opción fabricar el componente en herramientas individuales con transporte manual o automático.
Registro en pilotos
Decisiones sobre la orientación de la parte y el tipo de transporte deben ser concurrentes tomando en cuenta una tercera consideración, el registro en los pilotos. El tipo, lugar, y número de pilotos afectan la progresión, la bobina y el tipo de transporte. La selección de pilotos comienza con el análisis de la configuración de la parte y las tolerancias requeridas. ¿Es posible o aceptable registrar los pilotos en agujeros dentro de la parte? Si una parte contiene agujeros, estos deben ser suficientemente para poderse usar con pilotos. Los agujeros de pilotos deben estar lo más apartados entre sí para que sea posible aumentar la exactitud de registro, adicionalmente éstos deben estar en el lugar
más apropiado si van a ser usados para estabilizar la tira y ayudar en el formado que se realiza en el troquel.
La tolerancias de los agujeros de piloto propuestos deben ser consideradas. Si la tolerancia del diámetro del agujero es muy cerrada, aun con un leve alargamiento causado durante el formado esto puede producir partes defectuosas. El alargamiento puede ser causada por algo muy simple como un viejo alimentador o uno que está un poco desajustado. Si un piloto se encuentra en
una parte que se recortará o en el esqueleto, un leve alargamiento es aceptable, siempre y cuando las dimensiones de la pieza de la parte se mantengan dentro de las tolerancias.
A veces, dos sistemas diferentes de pilotos pueden ser requeridos. En estas aplicaciones, ambos conjuntos deben ser perforados al mismo tiempo para poder
proveer transiciones exactas desde el primer conjunto de pilotos al segundo. Cuando está implicada una cantidad significativa de la carrera del botador pueden ocurrir problemas. Los pilotos pueden tocar el material al mismo tiempo que se alinea la tira. Si se requiere una carrera considerable de botador, los pilotos rozarán los agujeros del piloto por la distancia completa de carrera.
Esto que puede causar rebabas en el agujero y conducir al rayado de los pilotos. La mejor solución es guiar el botador y colocar los pilotos en el botador.
Salida del troquel
A menudo se pasa por alto la manera que la parte saldrá de un troquel hasta que se llega el final del diseño. Esto es a veces, el factor determinante para el diseño de un troquel. Remover la parte del dado puede requerir girar la parte, usar un tipo diferente de transportador, o cambiar la secuencia de operaciones dentro del dado.
Las posiciones de las formas en la parte y su relación para donde la parte es transportada, tienen un efecto directo en donde o en cómo sacar la parte del dado. Una tira tipo escalera provee el método más fácil para remover la parte del dado. Generalmente, la parte puede ser cortada y se le puede hacer un corte de
silueta a través del dado.
Se deben considerar varios factores cuando un dado se diseña para que las partes puedan ser cortadas y se les pueda permitir caer en el extremo. Por ejemplo, el peso de la parte debe ser suficientemente des balanceada para permitir que caiga fuera del bloque del dado. Un perno de recorte puede ser agregado al pisador superior para asegurar que la parte salga del dado.
Si se forman orillas o bridas bajo la parte se deben agregar claros. Si esto no es posible, puede ser necesario rediseñar el dado para asegurar la salida de la parte. Si se forman orillas hacia arriba son formados para arriba, el avance de la tira a veces va a botar la parte del dado.
Determinando el número de progresiones:
Una vez que el diseño es determinado, el número exacto de estaciones necesarias pueden ser evaluados. Es importante mantener la construcción del dado en
mente cuando se finaliza la el diseño de la tira.
Usualmente, se deben incluir estaciones vacías para prevenir el debilitamiento del dado si se requirieran otras modificaciones. Además, la facilidad de mantenimiento de una herramienta se debe siempre tener en cuenta.
Mientras aumenta la complejidad de la herramienta, el grado de confianza en el diseño también juega un rol al decidir cuantas estaciones deben ser incluidas. Si
surgen dudas ya sea sobre si la parte esta propiamente dibujada o si la forma saldrá de la manera deseada, se deben agregar uno o más estaciones vacías, entre mayor es la incertidumbres, mayor es el e números de estaciones vacías que deben agregarse.
Si se construye el dado sin estaciones vacías y se tienen que agregar operaciones adicionales, las opciones son pocas. El casi todos estos casos la integridad del dado puede ser comprometida para acomodar la modificación. A menudo, se tiene que construir condiciones de mantenimiento no deseadas en el troquel. Cualquiera de estas situaciones puede producir un dado que se rompe repetidamente y es costoso para mantener.
Conclusión:
Lograr mantener los fundamentos es clave para producir calidad, dado y partes rentables. Entre más complejo sea el dado, más importante son las decisiones sobre los fundamentos. Con una evaluación apropiada y compromisos apropiados, se puede determinar la mejor opción. Esto producirá un troquel fuerte con buena alimentación y de fácil mantenimiento. El dado pude producir una calidad constante de la partes para imprimir. La decisión propia debe proveer el mejor valor para la herramienta.
Traducido por Samantha Vazquez Vázquez
Revisión Técnica: Dr. Víctor Hiram Vazquez Lasso
Revisión Técnica: Dr. Víctor Hiram Vazquez Lasso
No hay comentarios:
Publicar un comentario